The crystals that can clean the planet
Source: cosmosmagazine.com
Matthew Hill’s work with the ultra-porous crystals known as metal-organic frameworks has earned him an Australian Prime Minister’s science prize.Some kids never outgrow their love of construction toys. CSIRO chemist Matthew Hill turned his love of blocks into a brilliant career – once he scaled down from Lego bricks to atoms. The materials he builds in the lab have won him the 2014 Malcolm McIntosh Prize for Physical Scientist of the Year, one of the five Prime Minister’s science prizes. The crystals might help solve some of the biggest problems on Earth, by soaking up CO2 from power plant emissions, acting as gas tanks for future fuels, or filtering contaminants from water supplies.
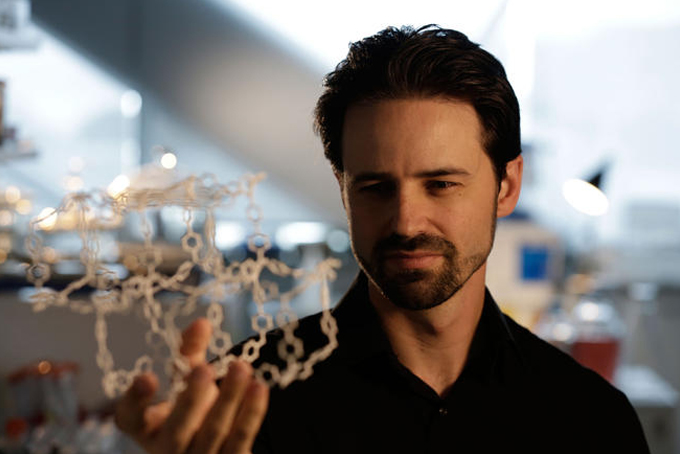
Matthew Hill still loves playing with building blocks, only these days they are atoms not Lego.Credit: WildBear
Hill has spent the last decade developing crystals known as metal-organic frameworks (MOFs). They look like ordinary white salt crystals. But X-rays reveal their secret. The MOF crystal is mostly empty space, 10 times more porous than anything else on the planet.
Chemists debate who made the first MOF. Some claim they date back to the 1950s. The argument was academic until the late 1990s when it first dawned on some researchers how useful these ultra-porous materials could be. They are the sponges of the atomic world – name your gas and they should be able to soak it up.
When Hill started out a decade ago, MOFs were in their infancy. Only tiny amounts had ever been made and chemists were still mastering how to fine-tune their properties for particular applications. Hill has earned the prize for helping to transform them into a tool for industry.
Imagine a material that soaks up carbon dioxide like a sponge and then wrings itself out to release the captured greenhouse gas for storage.
If you X-ray an MOF it resembles a scaffold-like construction toy called Tinkertoys. The struts are made of organic components and metal atoms form the joints. They look like stacks of nanoscale cages.
By using different metal and organic components, Hill can customise these cages for various purposes. To store hydrogen – the application with which Hill started out – you might make the holes a little smaller to make sure the cages are a snug fit for the diminutive gas molecules. So strong is the interaction between cage and gas it needs heat or a vacuum to suck the gas back out – a far safer way to store hydrogen than compressed in a tank, which will explode if ruptured.
Hill’s MOFs look like salt crystals until X-rays reveal their secret structure. Credit: WILEY-VCH Verlag GmbH & Co. KGaA, Weinheim
Or you can give your MOF some smarts so it responds to certain stimuli. Imagine a material that soaks up CO2 from power-plant flue gas like a sponge and then, when exposed to sunlight, wrings itself out to release the captured greenhouse gas for storage. Hill’s CO2-capturing MOF uses organic linkers that switch shape when exposed to UV light to squeeze out captured gas. “About 80% of the gas came out straight away,” Hill says. That’s remarkably efficient given that conventional carbon-capture materials require so much heat to release the captured gas they can sap 20% of the power generated by the plant.
Using sunlight probably isn’t going to be a practical solution for industry-scale carbon capture, but Hill says he is examining alternative smart MOF materials that will release the gas in response to other triggers.
When Hill began his work almost a decade ago, the idea of making a hydrogen fuel tank from MOFs was just a dream. “To make one gram of the material was a major undertaking,” he says. So he scaled up by designing a “flow reactor” – the raw ingredients are piped into one end of a heated tubular reactor where they mix together under carefully controlled conditions, and finished product flows steadily out of the other. With this set-up he can make 460 grams per hour.
The next version of his reactor is 10 times bigger. The easier MOFs are to make, the cheaper they become. When MOFs first went on sale a few years ago, in research-scale quantities, they cost $100 per gram. Hill expects his reactor to collapse that price 10,000-fold. “Once we are in that range, maybe it is applicable for industry,” he says.
One strand of Hill’s work is being closely watched by industry. In addition to gas storage MOFs have another useful property. Thanks to their regular structure, with identically sized holes throughout, they make excellent sieves, ideal for cleaning out the nitrogen and CO2 impurities in natural gas.
Industries use porous membranes to sieve these contaminants before natural gas is piped to homes and factories. But they quickly break down and need to be replaced within weeks. Incorporating MOFs into the membranes will strengthen the structure, extending lifespans to a few years.
These long-lived gas-separation systems have impressed Christian Doonan, an MOF researcher at the University of Adelaide. “They could lead to step-change developments in industrial processes,” he says. But really, the industrial possibilities for MOFs are endless, he adds. “The first MOF was only published in 1998, so the field is only 15 years old, it’s still growing.”
Hill agrees. “Their use is limited only by our imaginations and our ability as chemists,” he says.
Source: cosmosmagazine.com